Overexertion Accounts For More Than 25% Of The Top Ten Injury Costs: Liberty Mutual
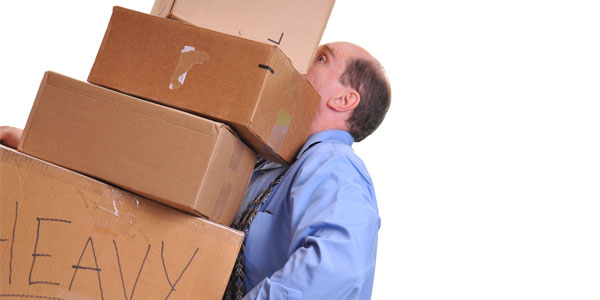
Produced annually, the Liberty Mutual Workplace Safety Index identifies the leading causes of the most disabling workplace injuries (resulting in six or more days of lost time) and ranks them by total Workers’ Compensation costs. The top five causes that accounted for 65.4% of the total injuries occurring in 2012 (most recent data available) were: 1) overexertion involving outside source, 2) falls on same level, 3) struck by object or equipment, 4) falls to lower level, and 5) other exertions or bodily reactions. Combined with your company’s worker injury data, the information can help prioritize preventive measures and training needs.
- Overexertion: Overexertion consistently tops the list. The category includes injuries related to lifting, pushing, pulling, holding, carrying, or throwing and represents $15.1 billion in direct costs, more than 25 percent of the overall national burden.
- Michael Smith, professor emeritus in the department of Industrial and Systems Engineering at the University of Wisconsin-Madison, notes that overexertion continues to be a problem because prevention requires a multidimensional and systematic approach including engineering design, training, organization, and supervision. He notes that everybody engages in lifting, pulling, pushing and carrying from the time they start walking to the time they come to the workplace and believe they can do it properly. Many employees simply do not understand the risk, although avoiding the danger can be as simple as getting help or using an assistive device.That’s why, in addition to assistive devices and administrative controls, employers should provide hands-on training, observe employees performing the tasks, offer guidance when they are doing it incorrectly and recognize that personal factors such as age, physical condition, and body weight will play a role. Supervisors should observe and interact with employees to ensure proper practices.Online ergonomic assessment risk tools to help businesses understand the risks associated with manual handling tasks can be helpful. For example, The NIOSH Lifting Equation is a tool used by occupational health and safety professionals to assess the manual material handling risks associated with lifting and lowering tasks in the workplace.The Liberty Mutual Research Institute for Safety updates its manual material handling (MMH) tables, commonly known as Snook tables to provide both male and female population percentages capable of performing manual material handling tasks without overexertion. Also, Washington State developed a series of checklists as part of a regulatory effort to control exposure to musculoskeletal hazards in workplaces.
- Falls on the same level: Ranking second with direct costs of $9.19 billion, the costs of falls on the same level have continued to rise for more than a decade. Slips and trips frequently precede this type of fall and causes include poor lighting, inadequate housekeeping, spills, ice, snow or rainwater, flooring or carpets in disrepair, uneven surfaces, lack of handrails, cords and cables and improper footwear. Distractions, inattention, texting, coordination and balance problems, age and medication usage can also be contributing causes.Notably, earlier studies indicate that employers perceive fall on the same level to be much less of a problem than it really is. Studying the trends and root causes of slips and falls at the workplace as well as periodic, rigorous self-inspections can result in fewer injuries and savings for employers.
- Struck by object: Taking the third place ranking was struck by an object. While many struck by object injuries occur on construction sites, they are also commonplace in offices. Distractions on and off the road, improper training of lift truck operators, overloaded high storage, inattention to job surroundings, opening doors, improper safety protocols and so on can put workers at risk of an injury.
- Falls to a lower level: Falls to lower level declined slightly in cost from 2011, but still totaled $5.12 billion. Many of the most severe fall accidents are associated with ladders, scaffolding, or some other elevation. Improper use of equipment, lack of handrails and slip-resistant treads for stairs, human error, technical failure or simply bypassing the need for fall protection are among the common causes. In addition to appropriate equipment and enforcement, employers should help employees understand the hazards, the serious consequences of shortcuts, and provide real scenarios of the exposure to falls. Proactively assessing and addressing risk at the start of a project not only reduces injuries but also reinforces a risk-aware culture.
- Bodily reaction: Bodily reaction, which includes injuries resulting from standing, sitting, slipping, bending, climbing, reaching or tripping, all without falling, ranked fifth at $4.27 billion. These injuries can occur when workers pull muscles, dislocate body parts or overstress joints while trying to prevent themselves from falling. They also commonly occur from awkward lifting, using stairs, or ladders with objects in their hands.
These five injury causes accounted for almost 65.4 percent of the total 2012 cost burden. Rounding out the top ten were roadway incidents involving motorized land vehicle (5.3 percent), slip or trip without fall (3.6 percent), caught in/compressed by equipment or objects (3.5 percent), repetitive motions involving micro-tasks (3.1 percent) and struck against object or equipment (2.9 percent).
Understanding injury causation is a complex process. Factors ranging from human error, unsafe behavior, stress, and inadequate skills to unsafe conditions, insufficient training, faulty equipment, lack of supervision etc. can come into play. It requires a continuous process of data collection and evaluation of preventive practices.
SEVEN SECRETS
You’ll receive important information to help you avoid overcharges on your workers’ compensation.